Blog
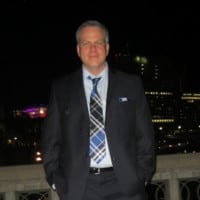
Brian Graydon | Mar 25 | 2 min read
How Automation in Laser Resistor Trimming is Meeting the Needs of Standard Production and Industry 4.0
Updated: Mar 25
As more and more electronics production facilities employ “lights-out manufacturing” concepts and move towards I4.0, becoming fully automated with little or no human presence, PPI’s RapiTrim laser resistor trimming systems are at the forefront of automation choices.
Manual Load
All RapiTrim systems can handle individual substrates up to 300×300 mm and can provide unique vacuum platen configurations as well as multi-up fixtures that cover a range of part sizes. Vacuum platen top fixture plates can be exchanged in seconds, minimizing unproductive overhead. With two fixtures, unloading and reloading of one fixture can occur while the second is being processed. This scheme provides high efficiency with much lower cost than full automation. Many different part sizes can be accommodated in this way.
Stack Loaders
Automatic part stack loading systems load and unload substrates with sizes up to 200×200 mm using a vacuum pickup. Cup locations are adjustable to accommodate small to maximum size substrates. Slipsheet handling is also available.
Systems contain two pickup heads, one for loading and one for unloading substrates. These substrate stacks (load and unload) are located at the front of the machine for easy access and exchange.
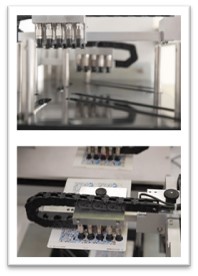
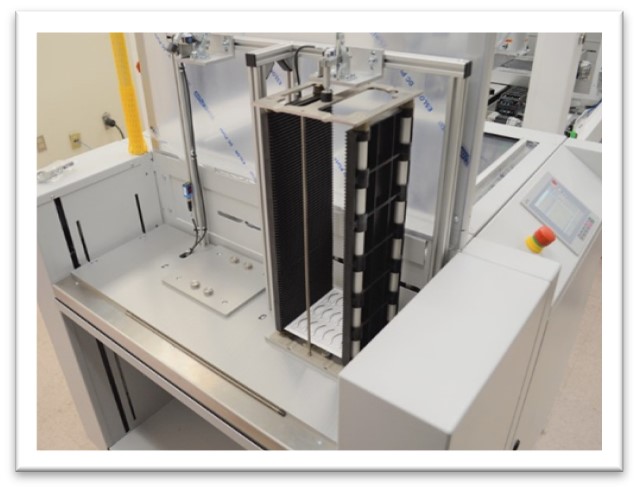
Magazine Loaders
For substrates handled in magazines, PPI offers SMEMA-compatible solutions compatible with a range of magazine automation suppliers. These handlers may be specified by the customer and PPI can supply them as part of a turnkey system.
Substrates may be exchanged quickly, and with the right choice of magazine handler the option of multiple magazines allows hours of efficient, uninterrupted operation. Loading is provided by a short conveyor which is followed by a robot pick-and-place onto a vacuum platen or special fixture for trimming.
The magazine loading system including external magazine-to-conveyor loaders and unloaders are fully integrated (mechanically, electrically and software integration) by PPI into the operation of the RapiTrim laser resistor trimming system. All controls are then available through the one advanced ProSys user interface. Single sided automation is also available.
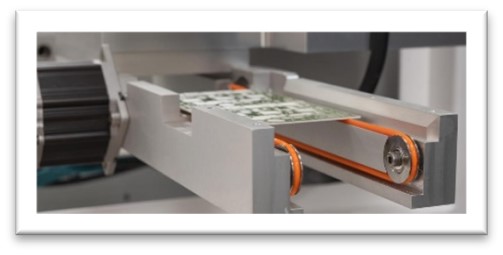
In-line Automation
An in-line conveyorized substrate transport is another available configuration. This would use the same SMEMA-compatible hardware as the magazine loader, just without the magazine loading / unloading modules. Substrates are passed to the RapiTrim directly on the conveyor track and picked-and-placed by the robot onto the vacuum chuck (or another fixture if necessary). As with the magazine loader configuration, full line integration is achieved by following SMEMA standards, and the transport controls are fully integrated into the RapiTrim user interface.
Custom Automation
If your requirements are not covered by one of the options above, don’t hesitate to contact PPI to discuss custom alternatives. PPI engineers can propose solutions for your unique needs, from custom fixturing to custom automation.
PPI Systems is a leading supplier of laser material processing and test systems. The company provides a broad range of turn-key solutions to the interconnect and electronic component market for via drilling, circuit processing, resistor trimming, and high-precision micro-machining.
